CFD-Simulation for the further development of a novel combustion system for biogenous residues
The target of the project is to further develop a novel combustion technology in the range of small to medium combustion capacity which uses a broad variety of applicable fuels on the base of regionally available, cost-effective biogenous residual materials. These materials comprise wheat-, barley-, corn- and rape straw, sunflower stems, municipal cut grass and bushes (lop), energy crops from fallow utilisation, palm leafs and many more. The research project will lead to a competitive and marketable combustion system using the named biomass fuels and implementing an innovative combustion concept developed in former research projects by the project partners.
The main aspects of the novel combustion concept imply the complete burnout of combustible material at comparatively low temperatures due to the usually low ash melting point of the used biomass fuels, the very short and uniform residence time of the gas phase in the combustion chamber resulting in very small and compact dimensions, and the highly turbulent flow within the combustion chamber creating excellent mixing of combustible gases and combustion air. Due to the fact that the combustion of the biomass fuel strongly depends on flow phenomena using the named novel combustion method, the design and the further optimisation of the combustion apparatus is based on extensive numerical flow simulations (CFD). These simulations are carried out using the commercial CFD-solver FLUENT on a multi-processor cluster-platform. Numerous advanced calculation models had to be applied to assure correct simulation results. These models concern the description of turbulence, radiation, homogeneous and heterogeneous biomass gasification and combustion and fly ash burnout. During the first part of the research project, the results of the simulations and the knowledge from former projects and plant operations have been used to tailor-fit the combustor geometry to the dimensions and details needed by the combustion reaction. After the build-up and commissioning of the real combustion power plant in a medium scale extensive experimental combustion analysis will be undertaken. This work will lead to a verification and fine-tuning of the used simulation methods. These refined simulations will be used for a further optimisation of the combustor geometry and the plant operational characteristics to maximise the thermal efficiency and to reduce the emissions like carbon monoxide, nitrogen oxide and dust. Additional analysis will include the identification of ‘hot spots’ inside the combustion chamber for choosing the proper steel grade for future plants as well as the detection of potential slagging and high temperature corrosion on the combustor surfaces.
The real combustion power plant will be operated using an automation system also developed by the research area Thermal Process Engineering and Simulation involving an industrial scale process controller (PLC), process visualisation, data acquisition and storage. Extended automation and control algorithms will be implemented to assure safe plant operation, fast and secure start-up, shut-down and emergency-stop procedures and an optimally controlled combustion within the plant. All important parameters concerning the combustion plant will be measured, stored and analysed to provide the background for further plant improvements.
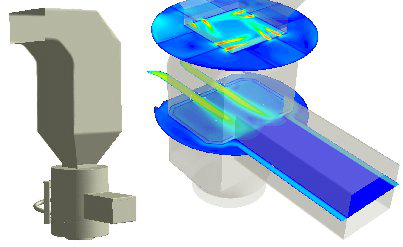
Figure: Exterior view of the combustion apparatus (left) and contour plot of gas phase velocity on two horizontal planes calculated from CFD-simulation (right)