Development, implementation and optimisation of a novel biomass combustion plant for polygeneration purposes
The combustion chamber is designed to utilise compressed bales made of herbaceous or fibrous biomass like wheat or maize straw, sunflowers or hay. The bale transporting drawer supplies the biomass fuel continuously to the primary combustion zone. In this zone the drying, devolatilisation and a part of the solid combustion takes place. In order to use the principle of air staging for limiting nitrous oxide emissions, this zone is operated with an excess air ratio of around 0,8. Two primary combustion air nozzles create highly turbulent free jets impinging the burning bale surface with high impact momentum. Thus, drying, devolatilisation and gas mixing is strongly increased. The secondary combustion zone is operated with appropriate excess air to oxidise the combustible gases emanating from the primary combustion zone. Complete burnout of gases has to be assured together with sufficient air staging to minimise emissions of CO, VOC and NOx. A number of air nozzles create turbulent free jets and a swirling gas flow in this zone. The remaining combustible solids drop from the primary zone to a small afterburning grate where the complete solid burnout takes place. The walls of the grate and the primary zone are not lined with refractory like in conventional combustion systems. The inner core is surrounded by an outer shell flowed through with the combustion air, which therefore is preheated and cools the walls (Miltner et al, 2005). This design offers a fast start-up process, however it needs an accurate and fast controlling system.
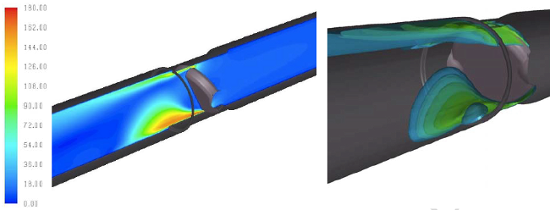
Contours of gas velocity magnitude (0-180m/s) around an exemplary control flap for gas flow measurement and control